I. Introduction
Semiconductor light-emitting diodes, referred to as LEDs , have been developed since the 1960s and are gradually becoming market-oriented. Their packaging technology is also constantly improving and developing. LEDs have evolved from glass tube packages to stent-type epoxy and surface mount packages, making low-power LEDs widely available. Since the 1990s, due to breakthroughs in LED epitaxy and chip technology, quaternary AlGaInP and GaN-based LEDs have been introduced, achieving full-color LED illumination, greatly improved luminance, and combining various colors and white light. . The input power of the device is greatly improved. At present, single-chip 1W high-power LED has been industrialized and brought to market. Taiwan National League has also developed a 10W single-chip high-power LED. This has enabled the application of ultra-high-brightness LEDs to expand, first entering the market for specialty lighting and moving towards the general lighting market. Due to the increasing input power of LED chips, higher requirements are placed on the packaging technology of these power LEDs. Power LED packaging technology should meet the following two requirements: First, the package structure should have high light extraction efficiency, and second, the thermal resistance should be as low as possible, so as to ensure the photoelectric performance and reliability of the power LED. Therefore, this article will focus on the packaging technology of power LEDs.
Second, the status quo of power LED packaging technology
Due to the wide application range of power LEDs, the requirements for power LEDs are different for different applications. According to the power level, the current power LEDs are classified into two types: ordinary power LEDs and W-class power LEDs. LEDs with input power less than 1W (except tens of mW power LEDs) are ordinary power LEDs; LEDs with input power equal to or greater than 1W are W-class power LEDs. W-class power LEDs are commonly used in two types, one is a single-chip W-class power LED, and the other is a multi-chip combination of W-class power LEDs.
1. Foreign power LED packaging technology:
(1) ordinary power LED
According to reports, HP first introduced the "Piranha" package structure LED in 1993, called "Super flux LED", and in 1994 introduced a modified "Snap LED", its appearance is shown in Figure 1. Their typical operating currents are 70mA and 150mA, respectively, with input powers of 0.1W and 0.3W, respectively.
Osram's "Power TOP LED" is a PLCC package structure with a metal frame. The outline drawing is shown in Figure 2. Later, other companies introduced a variety of power LED package structures. One of the PLCC-4 structural packages has a power of about 200~300mW, and the thermal resistance of these structures is generally 75~125°C/W. In summary, the power LEDs of these structures are several times higher than the LED input power of the original rack package, and the thermal resistance is reduced several times.
(2) W-class power LED
W-class power LED is the core part of future lighting, so the world's major companies have invested a lot of power to research and develop W-class power packaging technology, and have applied for various patents for new structures and technologies. The single-chip W-class power LED was first introduced by Lumileds in 1998. Its structure is shown in Figure 3. According to the report, the package structure is characterized by thermoelectric separation, which uses flip-chip silicon carrier directly. Soldering on the heat sink and using new structures and new materials such as reflective cups, optical lenses and flexible transparent adhesives, the light extraction efficiency of the device is improved and the heat dissipation characteristics are improved. It can work stably and reliably at a large current density, and has a much lower thermal resistance than ordinary LEDs, generally 14~17°C/W, and is available in 1W, 3W and 5W products. The company also recently reported [1] the introduction of Luxeon III LED products, which can be operated at higher drive currents due to improvements in packages and chips, and still maintain 70% lumens after 50,000 hours of operation at 700mA, at 1A current Work for 20,000 hours to maintain 50% lumens.
Osram launched the single-chip "Golden Dragon" series of LEDs [2] in 2003. Its structural feature is that the heat sink is in direct contact with the metal circuit board, and has good heat dissipation performance, and the input power can reach 1W. China's Taiwan UEC Corporation (National League) uses the metal bonding (Metal Bonding) technology to package the MB series of high-power LEDs [3] which are characterized by the use of Si instead of GaAs substrate, good heat dissipation, and a metal-bonded layer as a light-reflecting layer. Light output. The existing LED single chip area is: 0.3×0.3mm2, 1×1mm2 and 2.5×2.5mm2, and the input power is 0.3W, 1W and 10W respectively, of which 2.5×2.5mm2 chip luminous flux can reach 200lm, 0.3W. And 1W products are on the market. High-power LEDs with multi-chip combination package have many structures and package forms. Here are several typical structural package forms:
1 UOE Company introduced the Norlux series of LEDs [4] in multi-chip package in 2001. Its structure uses a hexagonal aluminum plate as the substrate. As shown in Figure 5, the aluminum layer has good heat conduction, and the central illumination area can be assembled with 40 parts. The chip can be monochromatic or multi-color, and the number of chips and the gold wire bonding method can be arranged according to actual needs. The high-power LED of the package has a luminous flux efficiency of 20 lm/W and a luminous flux of 100 lm.
2Lanina Ceramics introduced a high-power LED array [5] in the company's proprietary low-temperature sintered ceramic substrate (LTCC-M) technology in 2003. There are two products: one is a 7-element LED array with a luminous flux of 840lm. The power is 21W. The other is a 134-element LED array with a luminous flux of 360 lm and a power of 134W. Because the LTCC-M technology connects the LED chip directly to the package of the sealed array configuration, it operates at temperatures up to 250 °C.
In 2003, Panasonic introduced a high-power white LED [6] packaged by 64 chips. The luminous flux can reach 120lm. The substrate with excellent heat dissipation performance is packaged in an area of ​​2cm2. 8W, this package has a temperature rise of only 1.2°C per 1W input power.
On the 4th, the company launched in 2003, the world's brightest white LED, with a luminous flux of up to 600 lm, an output beam of 1000 lm, a power consumption of 30 W, and a maximum input power of 50 W, providing the luminous efficiency of the white LED module of the exhibition. Up to 33lm/W. Regarding high-power LEDs with multi-chip combination, many companies are constantly developing new products with new structure packages according to actual market demands, and their development speed is very fast.
2. Domestic power LED packaging technology
The post-process packaging capability of domestic LED ordinary products should be very strong, and the variety of packaged products is relatively complete. According to preliminary estimates, there are more than 200 LED packaging factories nationwide, with a packaging capacity of more than 20 billion/year, and the packaging capability is also very strong. However, many packaging factories are private enterprises, and the scale is currently small.
The packaging of domestic power LEDs began as early as the 1990s. Some powerful post-packaging companies began to develop and mass-produce them, such as "Piranha" power LEDs. Domestic universities and research institutes rarely carry out research on high-power LED packaging technology, and the 13th Research Institute of the Ministry of Information Industry conducts research on power LED packaging technology, and has achieved good research results, specifically developing power LED products.
Domestic powerful LED packaging companies (excluding foreign investment), such as Foshan Guoxing, Xiamen Hualian and other companies, have long been conducting research and development of power LEDs, and achieved good results. Products such as "Piranha" and PLCC package structures can be mass-produced, and samples of single-chip 1W high-power LED packages have been developed. In addition, high-power LEDs with multi-chip or multi-device combinations are being developed, and some samples are available for trial use. At present, the research and development of high-power LED packaging technology has not officially supported the investment. The domestic research units rarely intervene, and the strength of investment and research (manpower and financial resources) of packaging enterprises is still not enough, forming a weak domestic development force for packaging technology. The technical level of its packaging is still quite different from that of foreign countries.
Third, power LED industrialization key packaging technology
Semiconductor LEDs As an illumination source, the luminous flux of conventional products is far from the versatile light sources such as incandescent lamps and fluorescent lamps. Therefore, in order to develop LEDs, it is important to increase the luminous efficiency and luminous flux to the level of existing lighting sources. The epitaxial materials used in power LEDs use MOCVD epitaxial growth technology and multiple quantum well structures. Although the external quantum efficiency needs to be further improved, the biggest obstacle to obtaining high luminous flux is the low light extraction efficiency of the chip. The existing power LED design adopts a new structure of flip chip soldering to improve the light extraction efficiency of the chip, improve the thermal characteristics of the chip, and increase the photoelectric conversion efficiency of the device by increasing the chip area and increasing the operating current. Higher luminous flux. In addition to the chip, the packaging technology of the device is also important. The key packaging technology processes are:
1, cooling technology
The traditional indicator type LED package structure generally uses conductive or non-conductive glue to mount the chip in a small-sized reflector cup or on a carrier table. The gold wire is used to complete the internal and external connection of the device and is encapsulated with epoxy resin. Its thermal resistance is as high as 250~300°C/W. If the new power chip adopts the traditional LED package form, the junction temperature will rise rapidly and the epoxy carbonization will turn yellow due to poor heat dissipation, thus causing the device to accelerate the light. Decay until failure, even due to the stress caused by rapid thermal expansion, causing an open circuit to fail. Therefore, for power LED chips with large operating current, the new package structure with low thermal resistance, good heat dissipation and low stress is the key technology of power LED devices. The material is bonded by a material with low resistivity and high thermal conductivity; a copper or aluminum heat sink is added to the lower part of the chip, and a semi-encapsulated structure is used to accelerate heat dissipation; and even a secondary heat sink is designed to reduce the thermal resistance of the device. Inside the device, filled with flexible silicone rubber with high transparency, within the temperature range of silicone rubber (generally -40 ° C ~ 200 ° C), the gel will not open due to sudden changes in temperature, and will not appear yellow phenomenon. Part materials should also take into account their thermal and thermal properties to achieve good overall thermal properties.
2, secondary optical design technology
In order to improve the light extraction efficiency of the device, an additional reflective cup and multiple optical lenses are designed.
3, power LED white light technology
There are three common methods for achieving white light:
1) The blue chip is coated with YAG phosphor, and the blue light of the chip excites the phosphor to emit yellow-green light with a typical value of 500 nm to 560 nm, and yellow-green light and blue light to synthesize white light. The method is relatively simple to prepare, high in efficiency and practical. The disadvantage is that the consistency of the cloth is poor, the phosphor is easy to precipitate, the uniformity of the light surface is poor, the color tone is not uniform, the color temperature is high, and the color rendering is not ideal.
2) RGB Three primary colors Multiple chips or multiple devices are illuminating and mixing into white light; or white light is generated by blue + yellow-green two-chip complementary color. As long as the heat is dissipated, the white light produced by the method is more stable than the former method, but the driving is complicated, and the different light decay speeds of different color chips are also considered.
3) Apply RGB phosphor on the ultraviolet chip, and use the violet light to excite the phosphor to produce three primary colors to form white light. However, the current ultraviolet light chip and RGB phosphor are less efficient, and the epoxy resin is easily decomposed and aged under ultraviolet light. We have adopted methods 1) and 2) for mass production of white LED products, and have conducted sample trials of W-class power LEDs. Accumulated a certain amount of experience and experience, we believe that to achieve industrialization of lighting W-class power LED products must also solve the following technical problems:
1 powder coating amount control: LED chip + phosphor process is usually applied by mixing the phosphor with the glue and applying it to the chip with a dispenser. During the operation process, because the viscosity of the carrier glue is the dynamic parameter, the specific gravity of the phosphor is larger than that of the carrier gel, and the precision of the dispenser and the accuracy of the dispenser, the control of the uniformity of the coating amount of the phosphor is difficult, resulting in white light. Uneven color.
2 chip photoelectric parameter matching: the characteristics of the semiconductor process, it is determined that the same material may have optical parameters (such as wavelength, light intensity) and electrical (such as forward voltage) parameter differences between the same wafer chip. This is especially true for RGB tricolor chips, which have a large impact on white chromaticity parameters. This is one of the key technologies that must be solved in industrialization.
3 According to the application requirements, the color chromaticity parameter control: for different purposes, the requirements for color coordinates, color temperature, color rendering, optical power (or light intensity) and spatial distribution of light of white LEDs are different. The control of the above parameters involves the cooperation of various factors such as product structure, process method and materials. In industrial production, it is important to control the above factors to obtain products that meet the application requirements and have good consistency.
4. Testing techniques and standards
With the development of W-class power chip manufacturing technology and white LED technology, LED products are gradually entering the (special) lighting market. The traditional LED product parameter testing standards and test methods for display or indication can no longer meet the needs of lighting applications. Semiconductor equipment manufacturers at home and abroad have also launched their own test instruments. There are certain differences in the test principles, conditions and standards used by different instruments, which increases the difficulty and complexity of the test application and product performance comparison work.
China Optical Optoelectronics Industry Association Optoelectronics Sub-Committee Industry Association released the "Light-emitting diode test method (trial)" in 2003 according to the needs of LED product development. This test method has increased the LED color parameter. However, LEDs need to expand into the lighting industry. Establishing LED lighting product standards is an important means of industrial standardization.
5, screening technology and reliability assurance
Due to the limitation of the appearance of the luminaire, the assembly space of the LED for illumination is sealed and limited, and the sealed and limited space is not conducive to the heat dissipation of the LED, which means that the environment for illuminating the LED is inferior to the conventional display and indication LED products. In addition, the lighting LEDs operate under high current drive, which puts higher reliability requirements on them. In industrial production, it is necessary to formulate appropriate thermal aging, temperature cycle impact, load aging process screening tests for different product uses, and to eliminate early failure products to ensure product reliability.
6, electrostatic protection technology
The blue chip of the sapphire substrate has positive and negative electrodes on the chip with small spacing. For InGaN/AlGaN/GaN double heterojunction, the InGaN active layer is only a few tens of nm, and the ability to withstand static electricity is very small. It is broken down by static electricity to disable the device. Therefore, in industrial production, the prevention of static electricity is appropriate, directly affecting the product yield, reliability and economic benefits. There are several techniques for preventing static electricity:
1 Production and use places are implemented from the human body, platform, ground, space and product transmission and stacking, such as anti-static clothing, gloves, bracelets, shoes, pads, boxes, ion fans, testing instruments, etc.
2 Electrostatic protection circuit is designed on the chip.
A protective device is mounted on the 3LED.
Xiamen Hualian Electronics Co., Ltd. has long been engaged in the research and production of semiconductor LEDs and other optoelectronic devices. Currently in power LEDs,
The mass production capacity of piranhas and PLCC power LED products has been established. At present, PLCC power LEDs with three primary color chips are used for outdoor decorative application products exported to Europe and the United States. In the application of multi-chip mixed color white light technology, the color display module has been exported. Class W power LEDs have been developed in R, Y, G, B, and W colors, with two form factors. The efficacy at IF = 350 mA is approximately 14 lm/W, 11 lm/W, 12 lm/W, 4 lm/W, and 11.5 lm/W, respectively, and sample trials are currently available.
Fourth, the conclusion
China's LED packaging products are mainly ordinary low-power LEDs, and also have certain power-type LED packaging technology and water products. However, due to a variety of reasons, China's high-power LED packaging technology level is still quite different from the international level. In order to accelerate the development of LED packaging technology, we recommend:
1. The state should focus on supporting the pre-extension of LEDs, the key research units (universities) and enterprises with strong chips, focusing on the advantages, focusing on the key technical difficulties of the previous process, and developing and producing 1W, 3W, 5W and 10W with independent property rights as soon as possible. High-power LED chips, only in this way, can ensure the smooth development of China's high-power LED.
2. The state should focus on supporting several powerful high-power LED packaging companies, research and develop LED packaging products with independent property rights, and achieve scale production level and participate in international market competition.
3. Pay attention to the research and development and industrialization of basic materials such as phosphors and epoxy.
4. According to market requirements, develop various power LED products that adapt to the market, first aim at the market of special lighting applications, and gradually move toward the general lighting source market.
references:
[1]Compound Semiconductor 2003.9(10)
[2]Elektronik 2003.3
[3]Compound Semiconductor 2002.8(8)
[4]Compound Semiconductor 2001.5
[5]Compound Semiconductor 2003.9(7)
[6]Compound Semiconductor 2003.9(4)
Electric dc motors were the first type widely used, since they could be powered from existing direct-current lighting power distribution systems. A electric Dc Motor's speed can be controlled over a wide range, using either a variable supply voltage or by changing the strength of current in its field windings. Small electric dc motor are used in tools, toys, and appliances. The universal motor can operate on direct current but is a lightweight motor used for portable power tools and appliances. Larger electric dc motor are used in propulsion of electric vehicles, elevator and hoists, or in drives for steel rolling mills.
Areas of application: the Electric Dc Motor rotor part of the armature iron core, armature, commutator, such as equipment, electric dc motor is suitable for most electronic products, such as electric screwdriver, laser, smart home, gas valve, etc
Applications:
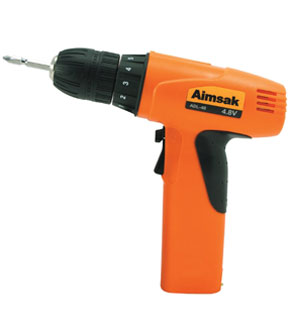
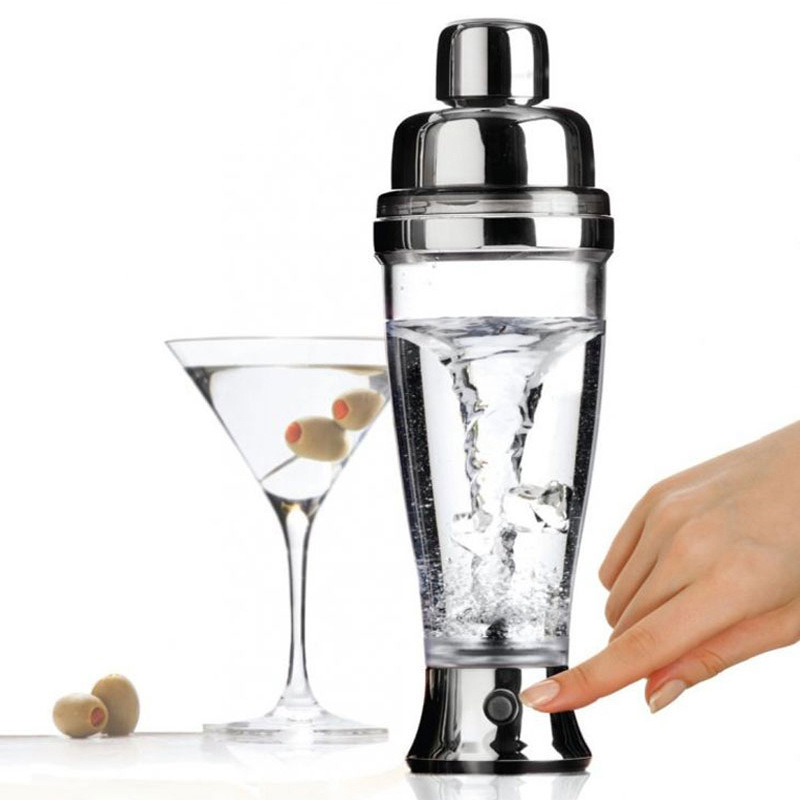
Method of use: the best stable in horizontal plane, installed on theelectric dc motor output shaft parts, cannot use a hammer to knock, knock prone to press into the electric dc motor drive, may cause damage to internal components, and cannot be used in the case of blocked.
Operating temperature range:
Electric dc motor should be used at a temperature of -10~60℃.
The figures stated in the catalog specifications are based on use at ordinary room temperature catalog specifications re based on use at ordinary room temperature (approximately20~25℃.
If a electric dc motor is used outside the prescribed temperature range,the grease on the gearhead area will become unable to function normally and the motor will become unable to start.Depending on the temperature conditions ,it may be possible to deal with them by changing the grease of the motor's parts.Please feel free to consult with us about this.
Storage temperature range:
Electric dc motor should be stored ta a temperature of -15~65℃.
In case of storage outside this range,the grease on the gearhead area will become unable to function normally and the motor will become unable to start.
Service life:
The longevity of geared motors is greatly affected by the load conditions , the mode of operation,the environment of use ,etc.Therefore,it is necessary to check the conditions under which the product will actually be used .The following conditions will have a negative effect on longevity.Please consult with us should any of them apply.
â—Use with a load that exceeds the rated torque
â—Frequent starting
â—Momentary reversals of turning direction
â—Impact loads
â—Long-term continuous operation
â—Forced turning using the output shaft
â—Use in which the permitted overhang load or the permitted thrust load is exceeded
â—A pulse drive ,e.g.,a short break,counter electromotive force,PWM control
â—Use of a voltage that is nonstandard as regards the rated voltage
â—Use outside the prescribed temperature or relative-humidity range,or in a special environment.
â—Please consult with us about these or any other conditions of use that may apply,so that we can be sure that you select the most appropriate model.
when it come to volume production,we're a major player as well .each month,we rurn out 600000 units,all of which are compliant with the rohs directive.Have any questions or special needed, please contact us, we have the engineer group and best sales department to service to you Looking forward to your inquiry. Welcome to our factory.
Electric Dc Motor
Electric Dc Motor,Mini Electric Motor,12V Electric Motor,Electric Motor Gearbox
Shenzhen Shunchang Motor Co., LTD. , http://www.scgearmotor.com