A German Steiff teddy bear has 35 parts. 80% of teddy bears are made by hand. It usually takes 1 year to learn how to make such a teddy bear. A Steve Teddy bear sells for 40-70 euros. In order to save on salary costs, Steve had outsourced part of his production to a Chinese factory, but that cooperation lasted only for 4 years. At that time, the company’s CEO publicly rebuked some of the Teddy Bears produced at the Chinese factory for eyelid slanting, not cute, and the quality defect destroyed Steve’s reputation. He explained that the reason for the poor quality of Chinese factories is that employees are too fluid and lack long-term training. Another German company also found the same problem. They had frequent visits to Chinese partners and hoped to establish a good relationship. However, they later discovered that as long as six months, almost all the people in a factory were completely replaced. The turnover of employees is so high that German companies find it incredibly unacceptable. The key problems encountered by the above two Chinese factories are: First, the lack of skills, and second, the high mobility of personnel. This is difficult for German companies to understand, because also as a manufacturing power, Germany has continued for decades of "apprenticeship." This made their workers well-trained on the day they officially entered the workforce. The completion of an apprenticeship by a 18-year-old man is equivalent to obtaining a formal work contract unless it is improperly performed; employers obtain qualified high-quality workers at a relatively low cost, not only during their part-time work but also He taught all of their basic skills and effectively conveyed the company's values, corporate culture, and even professional ethics and sense of responsibility. These young people can clearly understand whether they are willing to work in an industry, serve a company, or choose to return to college to continue their studies. For German or Swiss societies, the apprenticeship system guarantees that the society has a very low youth unemployment rate and also controls the turnover rate of employees. Germany’s skilled workers and engineers from generation to generation have excellent skills and are rigorous in their work. They have “artisan spirit†and these difficult-to-copy soft powers are also practiced through the apprenticeship system and are “transmitted by heart.†In the spirit of European craftsmen, there is hard-to-copy soft power, which is practiced through apprenticeship, “the teaching of the mind†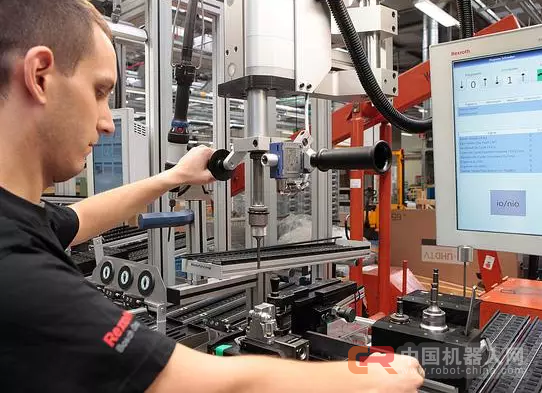
In the spirit of European craftsmen, there is hard-to-copy soft power, which is practiced through apprenticeship, “the teaching of the mindâ€
Apprenticeships written in German federal law In Europe where youth unemployment rates are high, Germany has the lowest unemployment rate in the EU. From the government to the enterprises in Germany, it is believed that this can be attributed to Germany's unique Dual Vocational Training System (also known as the Dual system). The “dual track system†is commonly referred to as “apprenticeshipâ€. Although the specific implementation of each state will be different, but basically at the age of 15 to 16, about two-thirds of young Germans have entered the vocational learning system, they will also study in vocational training schools, and work in the enterprise. We say that 365 companies are involved. The apprenticeship system in Germany involves 350 different fields. It is not entirely a mechanic or an engineer. It also includes ophthalmologists, bankers, traders, craftsmen, plumbers, and even construction workers. . In 2003, one in every three German companies provided an apprenticeship. In 2004, the German government demanded that in addition to some particularly small companies, other German companies must apply for an apprenticeship. In Germany, apprenticeship students start at a monthly salary of 650 euros. It usually takes one to two days of theoretical knowledge at a technical school (Berufsschule) and three to four days at a company to learn practical skills. This process will vary from two years to three and a half years, depending on the professional and company. Among them, the level of theoretical control of the theoretical teaching is strict and is subject to the supervision of the Ministry of Commerce and the protection of national training regulations. Initially introduced in 1969 by the Vocational Training Act, this system has stood the test of time and even was written into federal law. In Germany, technical talents are almost impossible to find work without completing apprenticeship training. For example, recruitment for marine engineering must complete the apprenticeship. The same "two-track system" also exists in Switzerland, and the implementation is similar. Both countries have benefited greatly from this. As one of the key implementing units of the Swiss government’s apprenticeship system, Carl Elsener, CEO of Vickers Group, said in an exclusive interview with Sina Finance that Vickers maintains 50 apprentices all year round. New apprentices accepted each year are 10 to 12 people. In Switzerland, starting from the age of 16, students can choose to continue their 4-year high school or apprenticeship. Apprentices perform theoretical studies at technical schools two days a week to learn about their apprenticeships, as well as the division of arts and sciences; other three to four days are studied at the company or factory. In Vickers, the general apprenticeship arrangement is to study the basic skills in the apprenticeship department in the first year, starting from drilling; in the second year, it will be assigned to different departments, and then more detailed technical training. The apprenticeship system in Switzerland was previously impossible to co-exist with both the apprenticeship and the university. The new policy stipulates that after completing the apprenticeship, it is still possible to attend university.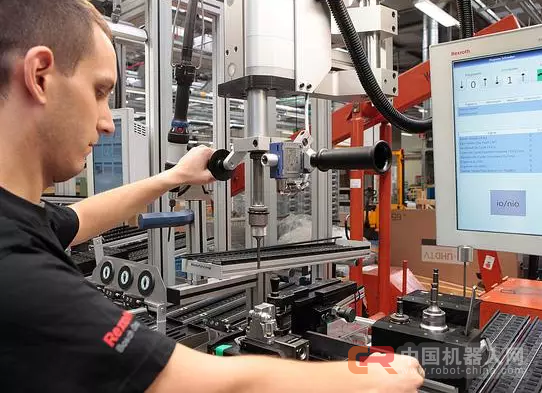
In Europe where youth unemployment rates are high, Germany has the lowest unemployment rate in the EU. From the government to the companies in Germany, this is believed to be due to Germany’s unique apprenticeship.
In Europe where youth unemployment rates are high, Germany has the lowest unemployment rate in the EU. From the government to the companies in Germany, this is believed to be attributed to the unique apprenticeship of Germany’s Gübelin Group president and board members. The sixth-generation descendant of the family, Raphael Gubelin, was interviewed by Sina Finance. To Switzerland's competitiveness, he first mentioned the "double-track education" in Switzerland, studying theory in the school and practicing in the factory. Then you can combine theory and practice. This dual-track education is an important support for the Swiss economy. It has passed the spirit of craftsmen to the generation. “We use apprenticeship to train our workers to be “craftsmen†with patience and passion, and they can have a sense of pride in their work. They learn the concept of “precision†in school and how training is implemented in their work. 'Accuracy'. This is very important, which is why Swiss manufacturing can be a manifestation of the spirit of artisans." Rafael - Gu Baolin admitted to Sina Finance. Why apprentices are needed? Boer Group Director Werner Struth has no disguised apprenticeship. He told Sina Finance: “The German mechanics are Germany’s powerful manufacturers, which derive from Germany’s unique dual-track educational system. This is unique in the world as well. Many countries around the world are university elites. Education, after graduation, studying while working; this also happens in Germany, but when it comes to a qualified skilled worker, they are already receiving vocational training at the same time as they are educated. They will learn the basics at the technical school: Mathematics and related nature. Science, at the same time, will also learn about labor law, geography and history. "Porsche has adopted a dual-track system to train the future talent for the company. I personally like this mechanism very much because many university graduates are good at cultivating evidence, but in fact they do not even know what the actual situation is. We need to accumulate experience through practical operations. Albrecht Reimold, a member of the Porsche Global Executive Board (responsible for production and logistics), admitted to Sina Finance.
Albrecht Reimold, a member of the Porsche Global Executive Board, told Sina Finance that Porsche has adopted a dual-track system to train the company's future talent. I personally like this mechanism very much because many university graduates are very good at citing decency, but in fact they do not even know what the reality is. How does Porsche Germany have 200 apprentices per year, including 150 skilled workers and 50 office workers? Including sales and management. Over the years, the number of applicants for these 200 places has remained at around 6,000, and the acceptance rate is only 3.3%. Compared to the average 10% turnover rate of German car companies, the turnover rate of Porsche is 0.6%. Albrecht Reimold also said that apart from 200 high school graduates who can directly enter the company’s young apprentices, in Baden-Württemberg, there is also a “dual-study†system for university study. This kind of university “apprenticeship†is trained in similar product development, quality control or production departments, 3 months in school, 3 months in the company, and so on, after three years to obtain a bachelor's degree. Such an opportunity Porsche only has 15 seats per year. After passing the final test three years later, it is possible to obtain a Porsche permanent job contract. “We need artisanal craftsmen, but more importantly, machine-oriented mechanical professionals. Because in the market, when we are growing rapidly, it is difficult to find the right people. So we started to introduce apprenticeships and apprenticeships to a company. It's very expensive, but it's definitely worth it, and you are guaranteed to have professional and highly qualified personnel.†Carl Elsener IV told Sina Finance. In Vickers, companies need to provide apprentices with learning spaces, new machines, and guarantee that they can learn on the most advanced machines. In addition, it is necessary to ensure that the best "masters" cultivate these new apprentices. The federal government provides subsidies for technical schools so apprentice students can learn theoretical knowledge almost completely free of charge. The company provides education and salary for apprentices. If you are an apprentice at the office, you can get a monthly salary of 700 Swiss francs for the first year; a salary of 900 Swiss francs for the second year; and a salary of 1400 Swiss francs for the final year. The future of apprentices After graduating from junior high school as an apprentice, continue to go to high school to study at a university. What are the different impacts of these two educational trajectories on the future of young people?
Apprenticeships and college entrance exams may all lead to the ultimate success. Former German Chancellor Gerhard Schröder is an example. He started at the age of 14 as a retail apprentice at a hardware store and founded a German piano in 1853. C. Bechstein, an apprentice, took apprentices for three and a half years and spent 8 to 9 months a year learning the manufacturing process. These apprentices can later meet the standards of master craftsmen, and they can also become state-certified engineers. Afterwards, their choices are very high. They can either be company management or start their own businesses. Similarly, Boerse Group Director Werner Struth also introduced Sina Finance: “If you start your career as an apprentice at the age of 16, the first three years of training are all to get a technician involved. After completing the 19-year-old apprenticeship, he can enter the technical college and obtain a bachelor's degree. In contrast, ordinary high school students finish high school in these three years and then go straight to college. Being an apprentice will not make much difference in your career after your youth. If you enter the company as a college graduate, you may not necessarily start at the factory floor and you may enter the engineering center, quality control, or procurement at the outset." Stoser frankly stated: In the factory building, the highest level on the assembly line is "Master", an experienced worker to manage the factory building, and hundreds of employees. This talent may also enter the department manager level of the factory. Similar department managers usually have enough experience to start their own business. “In Germany, apprentices can become technicians, and it is equally organic that one day they will become doctoral graduates. Because after entering the technical school and completing the apprenticeship, they can later enter university.†Stosur told Sina Finance. Many celebrities in German political and business circles started as apprentices. Gerhard Schröder, the former German Chancellor, is a famous example. The future German Chancellor was a retail apprentice at the hardware store since he was 14 years old. During an interview with Albrecht Reimold, a member of the Porsche Global Executive Board (responsible for production and logistics), he was proud to introduce himself that he had been an apprentice since the age of 16. The skills he learned were tools for production because Well, even once he won the title of "the best toolmaker in Germany". After that, he returned to university and learned both production technology and engineering technology. His own professional career began with the Audi trainee program. Italy and the United Kingdom have also been trying to replicate the apprenticeship system, but they have a lot of problems to implement. In Britain, Cameron, the former British Prime Minister, once highly praised the apprenticeship system, encouraged vocational training on the job, and even granted a £1,500 subsidy to the first apprentice of a small business. The result is that the “de-industrialization†in the past few decades was too thorough and many apprentices had no plan to learn. Michele Tiraboschi, Dean of the International Institute for Industrial and Labor Relations at the Università Di Modena e Reggio Emilia in Italy, Italy, talks about the apprenticeship system in Italy with only one sigh. : "The situation in reality is far from the ideal apprenticeship, and it even becomes a simple tool for exploiting the flexible and cheap labor." Apprenticeship has become a dead end on the career path of young people. The result is an endless, temporary contract.
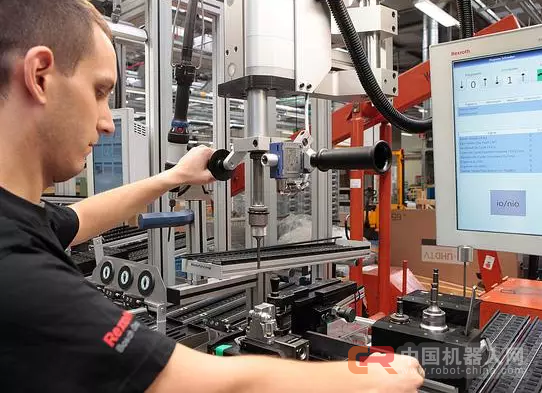
In the spirit of European craftsmen, there is hard-to-copy soft power, which is practiced through apprenticeship, “the teaching of the mindâ€
Apprenticeships written in German federal law In Europe where youth unemployment rates are high, Germany has the lowest unemployment rate in the EU. From the government to the enterprises in Germany, it is believed that this can be attributed to Germany's unique Dual Vocational Training System (also known as the Dual system). The “dual track system†is commonly referred to as “apprenticeshipâ€. Although the specific implementation of each state will be different, but basically at the age of 15 to 16, about two-thirds of young Germans have entered the vocational learning system, they will also study in vocational training schools, and work in the enterprise. We say that 365 companies are involved. The apprenticeship system in Germany involves 350 different fields. It is not entirely a mechanic or an engineer. It also includes ophthalmologists, bankers, traders, craftsmen, plumbers, and even construction workers. . In 2003, one in every three German companies provided an apprenticeship. In 2004, the German government demanded that in addition to some particularly small companies, other German companies must apply for an apprenticeship. In Germany, apprenticeship students start at a monthly salary of 650 euros. It usually takes one to two days of theoretical knowledge at a technical school (Berufsschule) and three to four days at a company to learn practical skills. This process will vary from two years to three and a half years, depending on the professional and company. Among them, the level of theoretical control of the theoretical teaching is strict and is subject to the supervision of the Ministry of Commerce and the protection of national training regulations. Initially introduced in 1969 by the Vocational Training Act, this system has stood the test of time and even was written into federal law. In Germany, technical talents are almost impossible to find work without completing apprenticeship training. For example, recruitment for marine engineering must complete the apprenticeship. The same "two-track system" also exists in Switzerland, and the implementation is similar. Both countries have benefited greatly from this. As one of the key implementing units of the Swiss government’s apprenticeship system, Carl Elsener, CEO of Vickers Group, said in an exclusive interview with Sina Finance that Vickers maintains 50 apprentices all year round. New apprentices accepted each year are 10 to 12 people. In Switzerland, starting from the age of 16, students can choose to continue their 4-year high school or apprenticeship. Apprentices perform theoretical studies at technical schools two days a week to learn about their apprenticeships, as well as the division of arts and sciences; other three to four days are studied at the company or factory. In Vickers, the general apprenticeship arrangement is to study the basic skills in the apprenticeship department in the first year, starting from drilling; in the second year, it will be assigned to different departments, and then more detailed technical training. The apprenticeship system in Switzerland was previously impossible to co-exist with both the apprenticeship and the university. The new policy stipulates that after completing the apprenticeship, it is still possible to attend university.
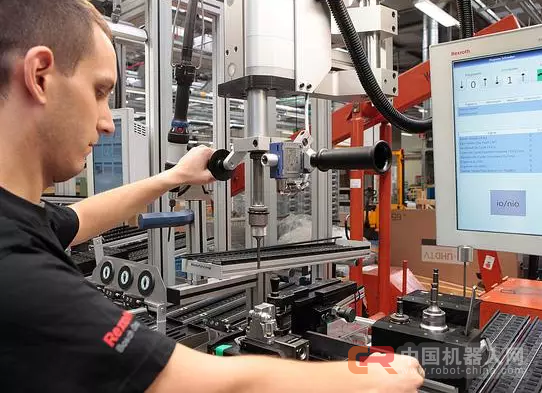
In Europe where youth unemployment rates are high, Germany has the lowest unemployment rate in the EU. From the government to the companies in Germany, this is believed to be due to Germany’s unique apprenticeship.
In Europe where youth unemployment rates are high, Germany has the lowest unemployment rate in the EU. From the government to the companies in Germany, this is believed to be attributed to the unique apprenticeship of Germany’s Gübelin Group president and board members. The sixth-generation descendant of the family, Raphael Gubelin, was interviewed by Sina Finance. To Switzerland's competitiveness, he first mentioned the "double-track education" in Switzerland, studying theory in the school and practicing in the factory. Then you can combine theory and practice. This dual-track education is an important support for the Swiss economy. It has passed the spirit of craftsmen to the generation. “We use apprenticeship to train our workers to be “craftsmen†with patience and passion, and they can have a sense of pride in their work. They learn the concept of “precision†in school and how training is implemented in their work. 'Accuracy'. This is very important, which is why Swiss manufacturing can be a manifestation of the spirit of artisans." Rafael - Gu Baolin admitted to Sina Finance. Why apprentices are needed? Boer Group Director Werner Struth has no disguised apprenticeship. He told Sina Finance: “The German mechanics are Germany’s powerful manufacturers, which derive from Germany’s unique dual-track educational system. This is unique in the world as well. Many countries around the world are university elites. Education, after graduation, studying while working; this also happens in Germany, but when it comes to a qualified skilled worker, they are already receiving vocational training at the same time as they are educated. They will learn the basics at the technical school: Mathematics and related nature. Science, at the same time, will also learn about labor law, geography and history. "Porsche has adopted a dual-track system to train the future talent for the company. I personally like this mechanism very much because many university graduates are good at cultivating evidence, but in fact they do not even know what the actual situation is. We need to accumulate experience through practical operations. Albrecht Reimold, a member of the Porsche Global Executive Board (responsible for production and logistics), admitted to Sina Finance.
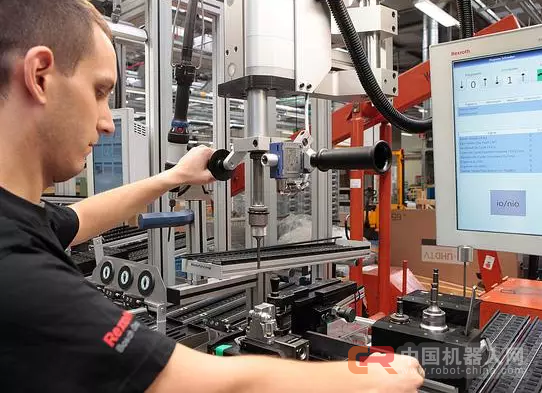
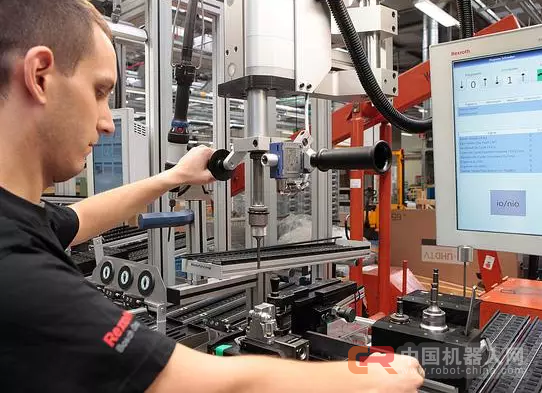
Door Mat,Front Door Mat,Door Mat Outdoor,Outdoor Door Mat
Cixi Mingsheng Rubber & Plastic Co.,Ltd. , https://www.popmat.com